How modern sorting, grading and packing solutions are making tomato packhouses more competitive
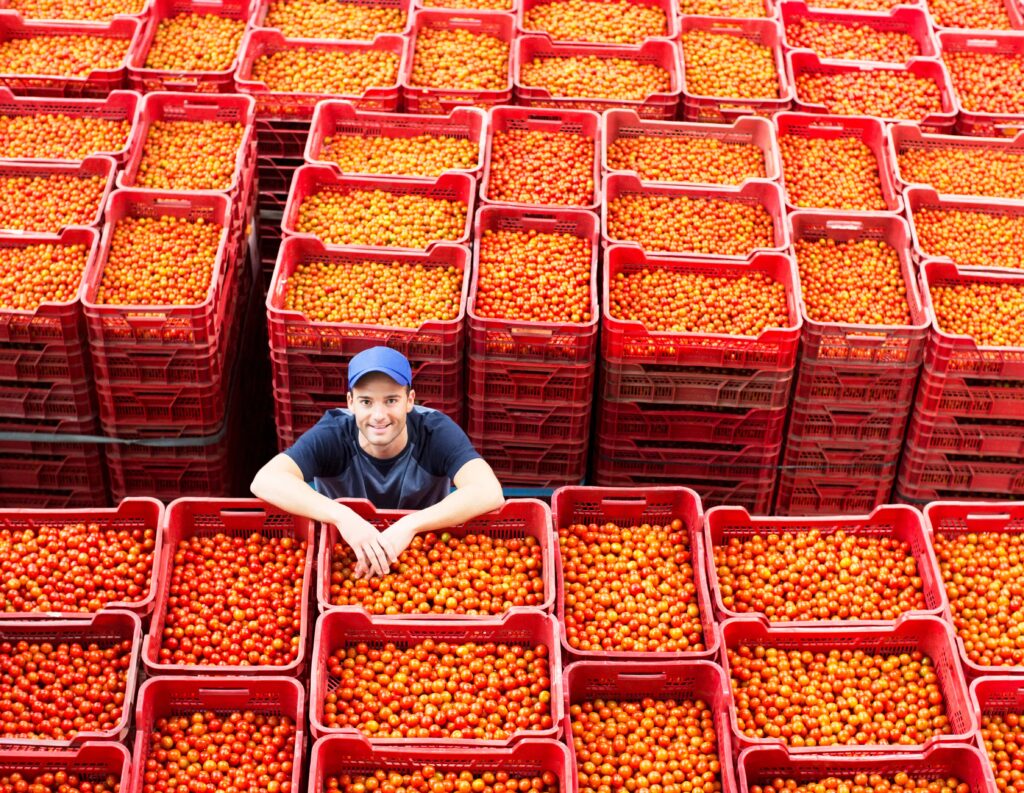
PRESS RELEASE
Tomatoes are one of life’s blessings. For growers, tomatoes give a high yield and are in strong demand. For consumers, tomatoes are packed with healthy antioxidants, nutrients, and vitamins. For processed food manufacturers, tomatoes add color, flavor, and natural goodness to juices, pastes, purees, sauces, and ketchup. And for food processing lines, tomatoes are a swelling revenue stream. But after counting the blessings, let’s pause for a reality check. While global demand for tomatoes is increasing, so are the pressures they bring to processing lines. There’s an urgent need to sort, grade, and pack ever-greater volumes of tomatoes during the short harvesting season without letting standards slip. Yet the shift in consumer preference towards greater choice in tomato varieties, especially smaller cherry tomatoes, makes the crop even harder to sort and grade. And at the same time as striving to increase throughputs, processors must also maintain or improve food safety and product quality – brand reputations depend on it. Busy processors also have to meet customers’ product specifications with measured precision: under-delivering can lose business; over-delivering erodes profits. Food waste also has to be minimized to optimize cost-effectiveness and demonstrate the commitment to sustainability that big retailers increasingly expect of their suppliers. All of this has to be accomplished even when specialized labor is difficult or impossible to find. These pressures are intensifying because tomatoes are gaining popularity and consumers are getting choosier. Demand is being driven upward by the spread of western diets and the rise of middle-class populations in developing nations. Demand has also been fired up by increasing awareness of healthy eating, a trend accelerated by the COVID-19 pandemic. As people idled away days during pandemic lockdowns, many will have worried about their health and browsed online information about healthy foods – and searching ‘tomatoes’ makes digital screens shine like the sun with positivity. This fruit is rich in lycopene, which can increase defences against cancer, heart disease, and other chronic diseases; in vitamins A, C, and E, which can benefit the immune system, bones, teeth, and skin; and in antioxidants that can help to fight off harmful free radicals in the body. What’s more, tomatoes are attractive, tasty, versatile, and conveniently portable. The booming popularity of tomatoes has led to the global production of approximately 190 million tons yearly, occupying some five million hectares of land. And when market researchers look ahead to the next five years, they see that the global sales of fresh and processed tomatoes will keep increasing at a compound annual growth rate of about 4-6%. Tomato growers of the past would be amazed by the crop’s current popularity. Though tomatoes were cultivated as long ago as AD 700 by the Incas and Aztecs in the Andes mountains, they were grown only in small volumes. When the fruit reached Europe in the 16th century, it was considered suspicious. Some Europeans wishfully believed tomatoes to be an aphrodisiac; many more thought the plant was poisonous and grew it only as an ornament. It wasn’t until about 1840 that people in western nations started to regard tomatoes as an edible crop, and it was another 80 years before global production really stepped up. The main reason for that big leap forward? Breakthroughs in mechanized processing. ‘Mission impossible’ is now possible In the years since tomatoes first became a widely sold food product, the key processing tasks of sorting, grading, and packing tomatoes have become much more complex. The introduction of new tomato varieties has brought a far greater range of differences in the fruit’s color, size, and shape. Retailers and consumers have raised their quality expectations to previously unobtainable levels. Exporting far across the globe has placed a premium on shelf life and the ability to forecast it. Yet two crucial measures of quality, firmness and Brix content, remain hidden from the human eye or cameras, and if the crop isn’t handled gently enough at any stage during processing, all quality can be lost. Dealing with these challenges might sound like a mission impossible – but a century since processing solutions kick-started the tomato industry, now they are helping it expand internationally by enabling processors to meet tougher market demands. Today’s state-of-the-art technologies empower tomato processors to increase throughput, reduce food waste, improve product quality, meet product specifications, maximize packout, reduce the problems associated with dependence on manual labor, and improve profitability. For many years now, the standard-setter in optical sorting and grading technologies for the food industry has been TOMRA Food. In the last five years, TOMRA has broadened its offering by acquiring two innovative New Zealand-based companies, BBC Technologies and Compac, so it is now the leading provider of integrated post-harvest-to-pack solutions. These take care of everything from tipping the fruit onto the line to packing it at the other end, and are well-suited to tomatoes. Because these solutions are modular and scalable, they can be tailored to businesses of all sizes. And because of TOMRA’s control software, they can be switched from one tomato variety to another with unrivaled ease and speed. (One exception is small, on-the-vine tomatoes, which still have to be sorted manually.) The TOMRA Food business area that designs, manufactures, installs, calibrates, and maintains post-harvest-to-pack solutions for tomato producers and packers is TOMRA Fresh Food. (The other business area is TOMRA Processed Food.) TOMRA has a good presence in the tomato market and is working to build on this, particularly in Latin America and Europe – and behind the scenes, TOMRA Food’s world-class R&D team is developing yet more innovations and technical solutions to help tomato producers and packers. Integrated post-harvest-to-pack solutionsTOMRA’s mission with tomatoes, as with other food categories, is to lead the resource revolution in a world where every piece of food counts. For large tomatoes, the company’s innovative, industry-leading solutions include the TOMRA 5S Advanced sorting and sizing platform, Spectrim sorter and grader, and UltraView inspection module or Inspectra² grading system as additional options. For small, snacking tomatoes, TOMRA offers two sorters, the MIRA360 and the Small Fruit Sorter (SFS) with InVision2 grading system. And for tomatoes of all sizes TOMRA provides a wide range of automatic weighing and filling solutions. All of these sorting and grading technologies are calibrated to each individual line’s needs. Through many years of experience working with processors and packhouses, TOMRA’s engineers have acquired a deep understanding of customers’ operational challenges and how to solve them. Customer-centricity is at the heart of everything TOMRA does, matching world-class technical expertise with an unrivaled global reach to provide local-level service and support. The TOMRA 5S Advanced, launched in 2021, is used for sorting and grading large tomatoes (with a minimum diameter of 40mm and a maximum diameter of 120 mm), by weight, size, shape, density, color, defects and softness. This machine builds on the class-leading performance of Compac’s Multi-Lane Sorter but was redesigned from the ground up. It’s the only platform truly designed for hygienic operation, with toolless cleaning and sanitization, and 100% stainless steel and food-safe polymer contact areas. And as its name suggests, this is the most advanced platform for sorting fruit. Unrivaled efficiencies are made possible by the machine’s specialized software features and connectivity to the data platform TOMRA Insight. The TOMRA 5S Advanced’s software features provide for optimization and efficiency across the line and include programs for element mixing, exact packout optimization, throughput control, and a Dynamic Lane Balancer which optimizes capacity when filling each lane and allows up to 10-15% more pieces of fruit per lane than other systems. These features can be controlled easily via the sorter’s intuitive graphic user interface. For handling smaller fruit sizes such as snacking tomatoes, the MIRA360 and SFS can sort into multiple streams by size and grades for color and defects, including softness. For large tomatoes, Spectrim first sorts according to surface blemishes, then grades on minor and major defects, including skin blemishes, insect damage, misshapen fruit, bruising, abrasions, and softness. Sorting parameters can be configured to grade for differing levels of defects, so that there’s full control when matching product grades to different markets. The UltraView inspection module integrates with Spectrim to take its ‘seeing’ power to the next level. With a dedicated set of high-resolution multi-spectral (color and infrared) cameras and LED lights located ideally close to the fruit and parallel to its direction of travel, this is the world’s most powerful fresh produce grading platform. Unfortunately, however, the skin of the fruit doesn’t tell its whole story. As we mentioned when referring to Brix and firmness, some crucial quality characteristics are hidden within. For this reason, TOMRA offers Inspectra², a non-invasive solution for internal defect grading. This platform’s near-infrared spectrometer can detect Brix, core rot, dry matter and firmness. These detection capabilities keep bad tomatoes out of a good box and reduce fruit giveaway. As the tomatoes near the end of the line, they are handled gently by TOMRA’s filling and packing machines. These automated solutions can simultaneously pack different grades of fruit for different markets. The CURO filling system – available with 2, 8, 12, and 16 filling stations – delivers consistent, high-speed filling at precise weights, with the flexibility to easily switch between a wide range of packing options. TOMRA offers several different types of bin and box fillers to ensure accurate, high-volume filling and accommodate various container sizes and weights. From one end of the pack line to the other, all these components are linked to communicate with each other to form an integrated solution. And connectivity to the cloud-based subscription service TOMRA Insight can make sorting machines the digital heart of processing and packhouse operations. Machine operators can respond instantly and easily to live data from TOMRA Insight to quickly improve line efficiencies; TOMRA’s engineers work closely with customers to analyze historic data which can unlock further efficiency improvements on the line and in the supply of raw materials. This means that TOMRA Insight opens a pathway to traceability from bin to pack and empowers packhouses to improve efficiencies by making better, data-driven decisions. This data is not only valuable today – it will also futureproof processing and packhouse businesses by meeting the industry’s evolving needs over the next 10 years or more. Just as processing technologies once provided the spark that got the tomato industry moving, now technical solutions are enabling businesses in this fast-changing industry to stay competitive and profitable. |
|
About TOMRA FoodTOMRA Food designs and manufactures sensor-based sorting machines and integrated post-harvest solutions transforming global food production to maximize food safety and minimize food loss, by making sure Every Resource Counts. These solutions include advanced grading, sorting, peeling and analytical technology to help businesses improve returns, gain operational efficiencies, and ensure a safe food supply. The company has more than 13,800 units installed at food growers, packers and processors around the world for Confectionery, Fruit, Dried fruit, Grains and Seeds, Potatoes, Proteins, Nuts, and Vegetables. TOMRA Food operates centers of excellence, regional offices and manufacturing locations within the United States, Europe, South America, Asia, Africa and Australasia. Follow TOMRA Food on: Facebook @TOMRA.Food Twitter @TOMRAFood Instagram @TOMRAFood LinkedIn at TOMRA Food. TOMRA Food is a division of TOMRA Group. TOMRA was founded in 1972 that began with the design, manufacturing and sale of reverse vending machines (RVMs) for automated collection of used beverage containers. Today, TOMRA is leading the resource revolution to transform how the planet’s resources are obtained, used and reused to enable a world without waste. The company’s other business divisions comprise TOMRA Recycling, TOMRA Mining and TOMRA Collection. TOMRA has approximately 105,000 installations in over 100 markets worldwide and had total revenues of about 12 billion NOK in 2022. The Group employs 5,000 globally and is publicly listed on the Oslo Stock Exchange. The company headquarters are in Asker, Norway.
|