Could irradiation protocols give Aussie exports a competitive edge?
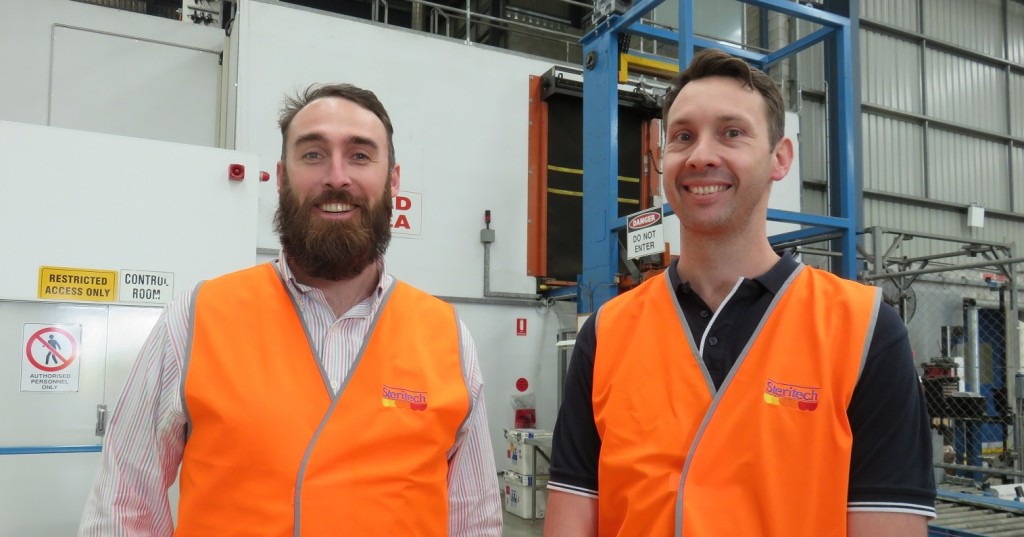
The Australian produce industry has achieved a string of irradiation protocols in recent years allowing for exports that keep the cold chain constant, are chemical-free and can make all the difference for freshness and premium pricing. But this is just the tip of the iceberg.Â
The bulk of Brisbane-based Steritech's irradiated products are not to do with fresh produce - medical equipment, sterilized packaging, beehives, and the list goes on.
But more than a decade ago the facility was the first globally to set up whole pallet irradiation specifically designed for fresh fruits and vegetables, and today it handles 3,000 metric tons (MT) of produce a year.
"We’ve seen exponential increases in tons treated. For the last three years this growth has averaged 50% annually," says export business development executive Ben Reilly.
"This is one of the most efficient treatment plants in the world – it’s been specifically designed with horticulture in mind, and we continue to pursue the latest technology in the area which is e-beam and X-Ray," he says, adding the facility currently uses gamma technology.
To put this volume in context, the plant has 60,000MT of capacity.
"It's a bit like saying we have one pallet in the container, with room to fit another 19," says Reilly.
The opportunity to fill this container is growing, starting with protocols in New Zealand which accepts five commodities - mangoes, litchis, papayas, tomatoes and capsicums (bell peppers) - and moving on to Malaysia for mangoes, Vietnam for citrus and table grapes, the U.S. for mangoes and litchis, and Indonesia for a whopping 44 different products.
"There’s also an irradiation protocol pending for Thailand," says Reilly.
"Thailand has historically been a good market for Australia but there were market entry restrictions affecting trade, particularly airfreight. A lot of people in the industry see irradiation as a valuable treatment option to reopen that airfreight window because it is fast, efficient, and cold chain-friendly.
"There is a pathway for persimmons to be approved for Thailand – the benefit is Australia will have established its first irradiation protocol potentially making it easier to add other items such as grapes and citrus," adds quality assurance officer Seth Hamilton.
These are all positive developments, but for the Steritech team and also the Australian industry, the big prize is North Asia.
China, Japan and South Korea allow a range of treatments for mainland Australian fruit but irradiation is not yet one of them. As an example, Reilly points out the recent success for Australian nectarine growers who gained access to China via a cold disinfestation and fumigation protocol.
"Fumigation is good because it is fast suited for airfreight, while cold treatment is good because it can treat large volumes.
"Unfortunately fumigation breaks the cold chain while cold disinfestation isa process that takes weeks. Irradiation has the ability to combine the benefits of both treatments without any of the major limitations."
He says irradiation is relatively fast, high volume and a chemical-free, gas-free treatment that does not require the cold chain to be broken.
"The current irradiation facility in Queensland can process product to fill a 40ft container in about an hour of machine time," he says.
"It's potentially the fastest treatment available and for our Australian growers who are looking to find a competitive edge in the premium markets it can be a massive advantage.
"Getting in early with airfreight-friendly protocols or a direct shipping line service equates to increased sales and program value which is what we saw in Vietnam with Australian grapes last season.
Reilly clarifies what the industry most needs are functional protocols and options, so while irradiation is very competitive he sees no problem with other treatment methods.
"We want a healthy industry with flexibility and options to choose the treatment for their product customer and the end consumer.
"It’d be great to get a protocol for Australia into North Asia because they are some of Australia’s strongest export markets.
"We support the industry and their approach with the Australian government to secure the most workable, effective and strategic protocols."
Reilly says government and industry representatives from some North Asian countries have shown a growing interest in the treatment option with several visits to the Steritech facility in Narangba, Queensland.
"Simply, we’re here to give Australia a competitive advantage and hopefully put our exporters a generation ahead in market access options, to help them develop workable protocols that are strategic today and still functional in 10-20 years’ time," he says.
"Rules, regulations and retail requirements often change with limited notice - packaging for example is becoming more and more involved in the marketing of fresh produce, and the prevention of food tampering or adulteration is important.
"Irradiation is a very effective treatment in that it’s an energy wave that can pass through sealed packaging, and or also treat for pests inside fruit, unlike gas options."
In terms of medical devices the equipment is treated for up to 35 hours at the Steritech facility, catering to the sterilization requirements of the health sector. Astronauts who travel into space eat irradiated food to the point of complete sterilization so it doesn't require any refrigeration.
Treating produce is very different. Firstly, the treatment itself will only go for 45 minutes to 1.5 hours, and the dose is extremely low.
"We purely treat for the phytosanitary purpose, but we have seen within that low treatment range it still has a very positive benefit in the reduction of naturally occurring bacteria and mold spores that would typically cause fruit to rot if you’ve left in the fridge too long for example.
"We see cherries and berries as two great examples where fruit can have days if not weeks of additional shelf life."
He says this presents an "amazing opportunity" to expand and improve the food supply chain and eliminate food waste.
"It’s a big deal, not only in a commercial sense, but in addressing the need to feed the world and efficiently manage our food production resources.
"It’s an option to complement good, clean food production, rather than fix an issue. We do not fix poor quality food or food sanitation issues, but we can enhance quality and food safety processes that are already in place."
How does it work?
We arrive at the Steritech facility during a relatively quiet period for the produce industry - right now, the only produce item to be treated is tomatoes for the New Zealand market, filling a supply gap when the country's production slows during winter.
The team however is already busy preparing for the grape, mango and litchi seasons in a few months' time.
The facility is essentially divided into two main areas - pre-processing and post-processing - divided by a fence with conveyor belts running along either side into a thick-walled concrete room.
Steritech has curtain docks installed for the trucks that arrive with produce so that the fruit and vegetables stay cool while unloading into cold rooms running at different temperatures.
From the new cold rooms, pallets are taken by forklift to the conveyor belt and then into the irradiation area.
Staff assist growers or traders to prepare the treatment with a quality assurance survey on arrival.
"This helps us ensure our customer has a good experience, and also that we make sure good fruit goes through the process and we’re able to maintain a strong reputation within the industry," says Hamilton.
Depending on the protocol for the fruit in question, an inspection may take place to check for any quarantine pests. Hamilton emphasizes the irradiation process will either kill or render infertile any pests, but for risk forecasting reasons there would ideally be none in the pallets.
"In reference to the U.S., seed weevil is a good example – even though irradiation is effective on it, it’s got to be from a field or farm that’s registered and has to be for all intents and purposes, pest-free.
"When we talk to growers, most would prefer to a protocol that requires some kind of registration and specific production requirements, as it promotes healthy markets with sales pre-planned or programmed generally limiting oversupply."
The pallets are loaded on to aluminum trays with a small device called a "dosemeter" which measures the irradiation dose throughout the process.
Once inside the room, the conveyor belt forms a U-shaped line around another smaller section where the pallet is treated. To cater specifically for the horticultural sector, the chamber has forced air cooling.
Once treated, trucks can pick up the pallets or alternatively they can be kept in one of two different temperature zones - for example, in mandarins this could be 2°C (36°F) or mangoes could be stored at 12-14°C (54-57°F).
Planning for a global future
With rigorous workplace health and safety standards, as well as innocuous fruit treatment, Reilly is hopeful for growth at Steritech for the benefit of the Australian produce industry.
Looking further down the track, Steritech is starting to engage and work with industry globally to help develop the utilization and potential for phytosanitary irradiation.
"In recent news this year, the U.S. shipped its first peaches to Mexico using phytosanitary irradiation. Although the U.S. has numerous import protocols using phytosanitary irradiation and it remains the second largest market for irradiated food, it has limited facilities customized to suit fresh produce treatment.
"There are a number of projects around the world that have built or plan to build new phytosanitary irradiation facilities in major production areas and markets including Peru, Mexico, Thailand and China.
"Steritech is focused on developing greater access in Australia for now, as Australia is one of the leaders in the field and has significant growth on the horizon."